Gear Pump Working Principle
sales01@cxflowmeter.com
The concept of a
gear pump dosing pump is very simple. Its most basic form is that two gears of the same size mesh and rotate with each other in a close-fitting shell. The outer diameter and both sides of the gear are tightly matched with the housing.
The material from the extruder enters the middle of the two gears at the suction port, and fills this space, moves along the housing with the rotation of the teeth, and is finally discharged when the two teeth mesh.
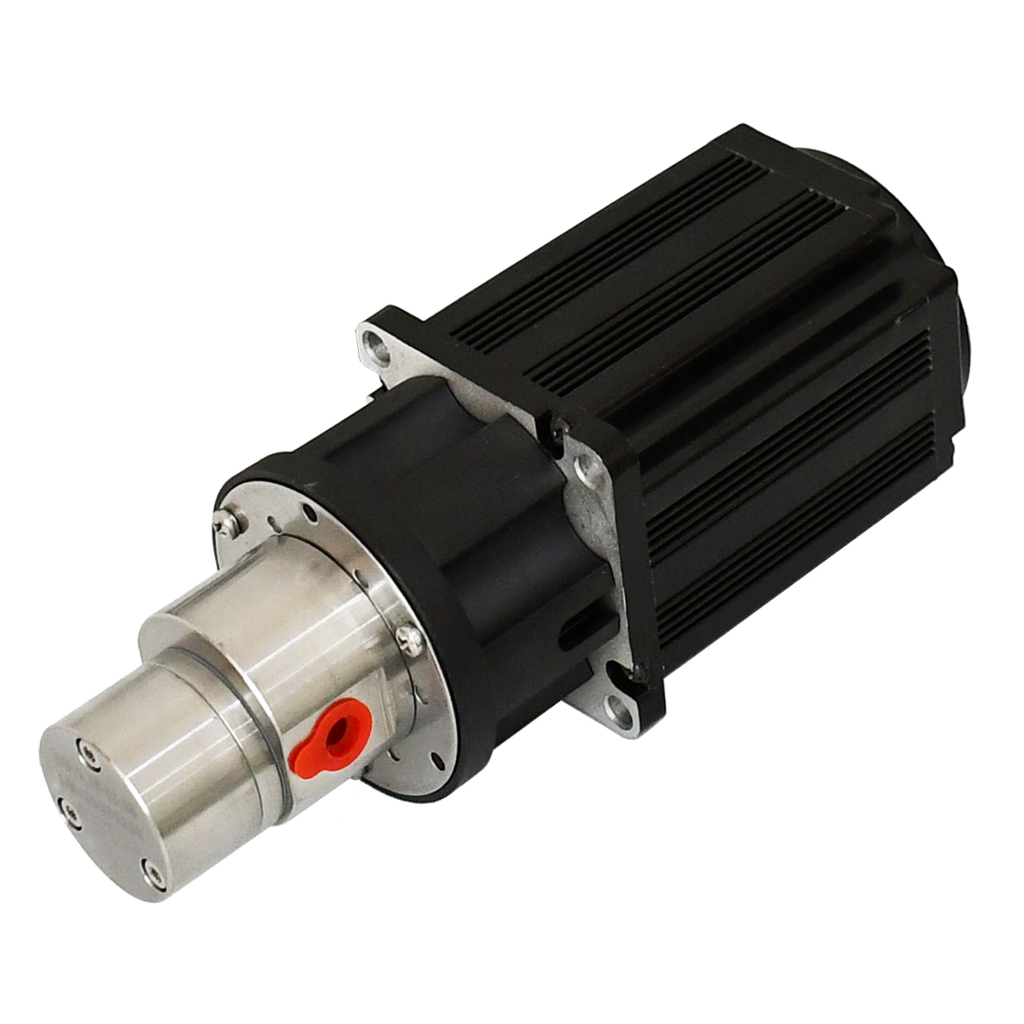
In terms of terminology, a gear pump is also called a positive displacement device, which is like a piston in a cylinder. When a tooth enters the fluid space of another tooth, because the liquid is incompressible,
the liquid and the tooth cannot be in the same Time occupies the same space, so that the liquid is mechanically squeezed out. Due to the continuous meshing of the teeth, this phenomenon occurs continuously,
so a continuous discharge amount is provided at the outlet of the pump, and the discharge amount is the same for each revolution of the pump. With the uninterrupted rotation of the drive shaft, the pump
continuously discharges fluid. The flow rate of the pump is directly related to the speed of the pump.
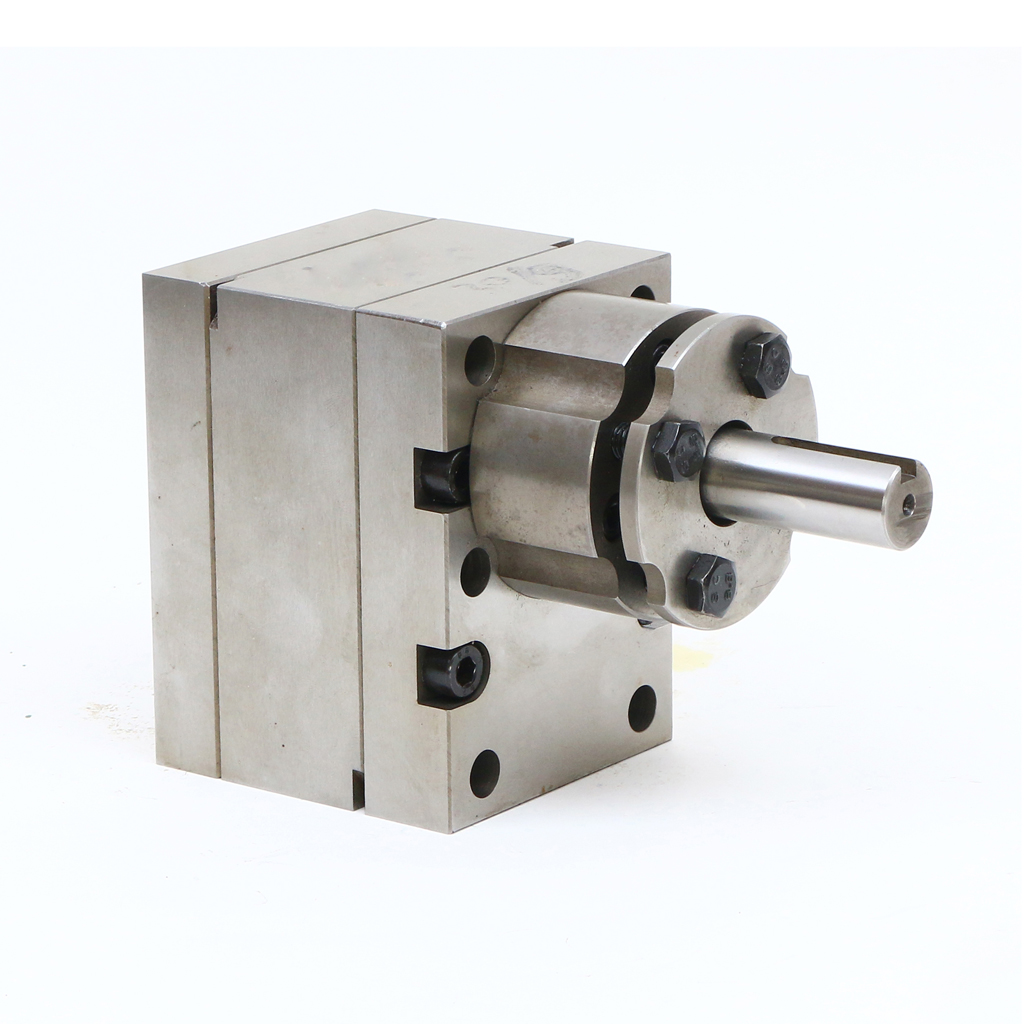
In fact, there is a small amount of fluid loss in the pump, because these fluids are used to lubricate the bearings and both sides of the gears, and the pump body can never fit without clearance, so 100%
of the fluid cannot be discharged from the outlet, so A small amount of fluid loss is inevitable, which prevents the pump's operating efficiency from reaching 100%. However, the pump can still run well,
and for most extruded materials, it can still reach an efficiency of 93% to 98%.
For fluids whose viscosity or density changes during the process, this pump will not be affected too much. If there is a damper, such as a strainer or a restrictor on the side of the discharge port, the pump
will push the fluid through them. If this damper changes during operation, that is, if the filter becomes dirty, clogged, or the back pressure of the limiter increases, the pump will maintain a constant flow rate
until the mechanical limit of the weakest part of the device is reached. (Usually equipped with a torque limiter).
There is actually a limit to the speed of a pump, which mainly depends on the process fluid. If the oil is conveyed, the pump can rotate at a very high speed, but when the fluid is a high-viscosity polymer
melt In physical activity, this restriction will be greatly increased.
It is very important to push the high-viscosity fluid into the two-tooth space on the side of the suction port. If this space is not filled, the pump will not be able to discharge the accurate flow rate. Therefore,
the PV value (pressure × flow rate) is another limiting factor, and It is a process variable. Due to these limitations, gear pump manufacturers will provide a series of products, that is, different specifications
and displacement (amount discharged per revolution). These pumps will be matched with the specific application process to optimize the system capacity and price.
sales01@cxflowmeter.com
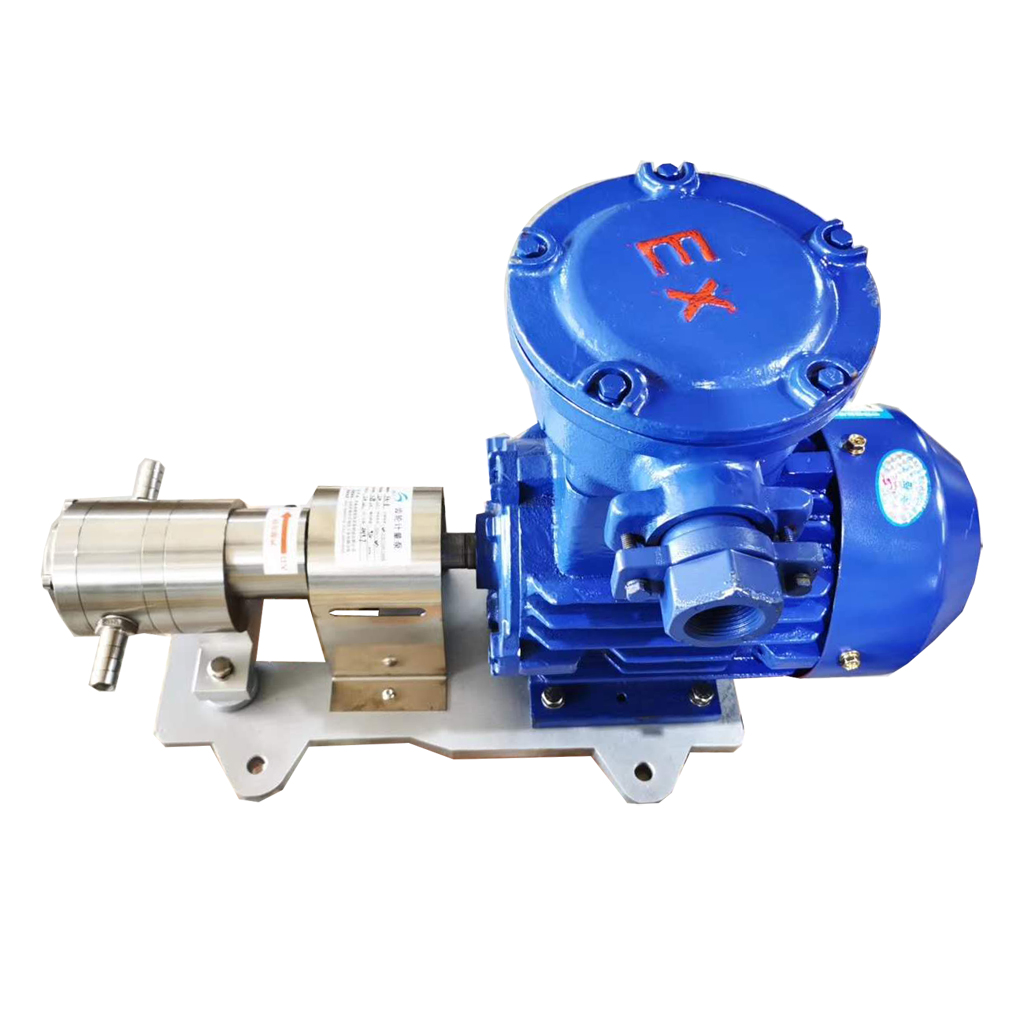
The gear and shaft of the PEP-II pump are integrated, and the whole body hardening process is adopted to obtain a longer working life. The "D" type bearing incorporates a forced lubrication mechanism,
allowing the polymer to pass through the bearing surface and return to the inlet side of the pump to ensure effective lubrication of the rotating shaft. This feature reduces the possibility of polymer retention
and degradation. The precision-machined pump body allows the "D" type bearing to be precisely matched with the gear shaft to ensure that the gear shaft is not eccentric to prevent gear wear.
Parkool seal structure and PTFE lip seal together form a water-cooled seal. This kind of seal does not actually touch the surface of the shaft. Its sealing principle is to cool the polymer to a semi-molten
state to form a self-seal. Rheoseal seal can also be used, which has reverse spiral grooves on the inner surface of the shaft seal, which can make the polymer back pressure back to the inlet. In order to
facilitate installation, the manufacturer has designed a ring bolt mounting surface to match the flange installation of other equipment, which makes the manufacture of cylindrical flanges easier.
The PEP-II gear pump has heating elements that match the pump specifications, which can be selected by users, which can ensure rapid heating and heat control. Different from the heating method in
the pump body, the damage of these components is limited to one board and has nothing to do with the entire pump.
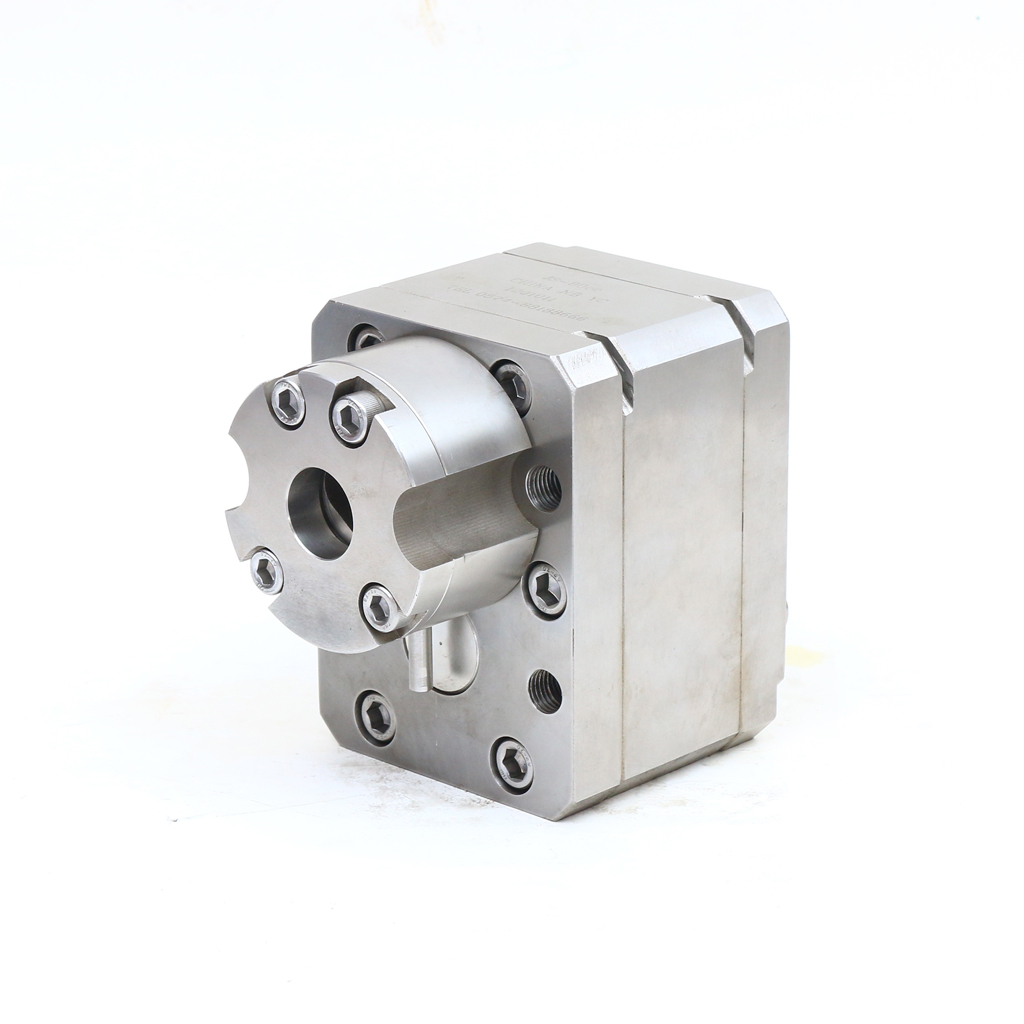
Drive device
The gear pump is driven by an independent motor, which can effectively block upstream pressure pulsation and flow fluctuations. The pressure pulsation at the outlet of the gear pump can be controlled
within 1%. Using a gear pump on the extrusion production line can increase the flow output speed and reduce the shear and residence time of the material in the extruder.
The external gear pump is the most widely used gear pump. Generally, the gear pump usually refers to the external gear pump. Its structure is shown in Figure 1, mainly composed of driving gear, driven gear,
pump body, pump cover and safety valve. The sealed space formed by the pump body, pump cover and gear is the working room of the gear pump. The axles of the two gears are respectively installed
in the bearing holes on the two pump covers, and the driving gear shaft extends out of the pump body and is driven by the motor to rotate. The external gear pump is simple in structure, light in weight,
low in cost, reliable in work, and has a wide range of applications.
When the gear pump is working, the driving wheel rotates with the motor and drives the driven wheel to rotate. When the meshing teeth on one side of the suction chamber gradually separate, the volume
of the suction chamber increases and the pressure decreases, and the liquid in the suction pipe is sucked into the pump; the suction liquid is pushed into the discharge chamber by the gear in the tooth groove
in two ways. After the liquid enters the discharge chamber, the gear teeth of the two gears continuously mesh, so that the liquid is squeezed and enters the discharge pipe from the discharge chamber.
The driving gear and the driven gear rotate continuously, and the pump can continuously suck and discharge liquid.
The pump body is equipped with a safety valve. When the discharge pressure exceeds the specified pressure, the conveying liquid can automatically open the safety valve to return the high-pressure liquid to the suction pipe.
The internal gear pump is composed of a pair of internal gears meshing with each other, crescent-shaped pieces, pump casings, etc. between them. The role of the crescent-shaped piece is to separate
the suction chamber from the discharge chamber. When the driving gear rotates, a partial vacuum is formed where the gears are disengaged, and the liquid is sucked into the pump to fill the teeth of the suction
chamber, and then enters the discharge chamber in two ways along the inner and outer sides of the crescent-shaped piece. Where the gear teeth enter the mesh, the liquid existing between the teeth
is squeezed and sent into the discharge pipe.
In addition to the characteristics of self-priming capacity, flow and discharge pressure, the gear pump has no suction valve and discharge valve on the pump casing. It has the characteristics of simple structure,
uniform flow and reliable operation, but it has low efficiency, high noise and vibration, and is easy to wear. , It is mainly used to transport various oils that are non-corrosive, non-solid particles and have lubricating
ability, and the temperature generally does not exceed 70 ℃, such as lubricating oil, edible vegetable oil, etc. The general flow range is 0.045-30ms/h, the pressure range is 0.7-20MPa, and the working speed is 1200-4000r/min.
Structural features
(1) Simple structure and low price;
(2) Low work requirements and wide application;
(3) The end cover and the inter-tooth grooves of the gear form many fixed sealed working chambers, which can only be used as a quantitative pump.
The gear adopts the new technology of the international advanced level in the 1990s-double arc sine curve tooth profile arc. Compared with involute gears, its most prominent advantage is that there is no
relative sliding on the tooth profile surface during the gear meshing process, so the tooth surface has no wear, running balance, no liquid trapping, low noise, long life, and high efficiency. The pump gets rid
of the shackles of traditional design, making the gear pump enter a new field in design, production and use.
The pump is equipped with a differential pressure safety valve as overload protection, and the total return pressure of the safety valve is 1.5 times the rated discharge pressure of the pump. It can also be
adjusted according to actual needs within the allowable discharge pressure range. However, this safety valve cannot be used as a pressure reducing valve for a long time, and the pressure reducing valve can be installed separately when needed.
The pump shaft end seal is designed in two forms, one is a mechanical seal, and the other is a packing seal, which can be determined according to specific use conditions and user requirements.
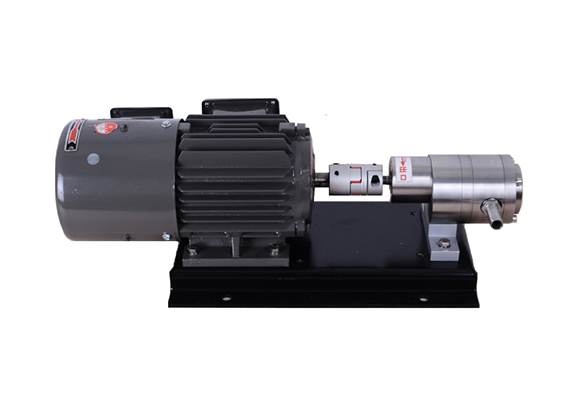
Classification of pumps
As far as the core component gears are concerned, they are mainly composed of common normal gear pumps and circular arc gear pumps. The common normal gear pump is more durable than the circular arc gear
pump when transporting impurities. The circular arc gear pump has a special structure, transports clean media, low noise, long life, and each has its own advantages.
If you want to know more related parameters and quotation of
metering pump, please contact winny:
sales01@cxflowmeter.com